EPLAN eVIEW: Faster maintenance
Cloud environments offer ideal conditions for networking with third-party systems. EPLAN eVIEW, available since 2019, surprises with an exciting showcase at the Hannover Messe – EPLAN and Festo will each be presenting a use case at their stand in which the reaction time for maintenance is considerably reduced. A fault during machine operations is signalled as a test case – and is quickly rectified.
Showcase with Festo
Cloud environments offer ideal conditions for networking with third-party systems. EPLAN eVIEW, available since 2019, surprises with an exciting showcase at the Hannover Messe – EPLAN and Festo will each be presenting a use case at their stand in which the reaction time for maintenance is considerably reduced. A fault during machine operations is signalled as a test case – and is quickly rectified. Monheim/Hanover, Germany, 01 April 2019 – The cloud as a central point of exchange for relevant engineering data provides a high-speed avenue for location-independent access to high-quality digital data. Festo has been an EPLAN partner for years and has numerous component data stored in EPLAN Data Portal. At the Hannover Messe, the provider of automation technology is presenting the modular demonstration system “Productivity Master” that maps the digital workflow from design to engineering through to maintenance and repair. This is right where EPLAN comes into play: The electrical engineering documentation is made directly available through EPLAN eVIEW. In concrete terms, the process looks as follows: In this joint showcase, the Productivity Master simulates a plant malfunction. And since time is money, downtimes can be optimised and/or shortened via good system integrations. How does this work? The fault is signalled on the Festo dashboards and communicated directly to the maintenance technician via the EPLAN Syngineer communications solution. In Syngineer, the technician can see the machine’s current status. This accelerates reaction times when faults crop up, thereby avoiding longer downtimes. Details of the electrical engineering documentation can be viewed in EPLAN eVIEW: The software makes the machine project available, and the error message directly displays the problem component using a jump function. This so-called “jump-in point” significantly shortens the time needed to fix a technical malfunction. For instance, manufacturing technicians or service technicians can use the redlining function to record information about changes in the schematics.
An example
A system sensor reports an electrical overload, which leads to a fuse being triggered. The first jump-in point is exactly this fuse, and the software reports this error to Syngineer. As a communications tool, Syngineer transfers this information to all the relevant departments. Regarding the specific fuse connections, EPLAN eVIEW is the “knowledge carrier” since the cloud-based software serves as the single source of truth. Another practical benefit is that only current data are available and changes are documented via a guided redlining workflow – eliminating sources of error once and for all. The advantages for operation speak for themselves: Whether a touchpad, a mouse or an active stylus, any sort of technology can be used and of course all common end devices as well – from PCs to touchscreens to mobile devices. This provides plenty of flexibility in a time when engineering is becoming increasingly globalised.
Exchange via Automation ML
Since control components in a system are becoming ever more common and valve terminals in particular are becoming more relevant for control systems, it became a practical requirement to ensure for greater and deeper integration in this area. In earlier versions of EPLAN Platform, it wasn’t possible to provide logic information about the complex valve terminals in the documentation. However, this is now possible with the current EPLAN Platform, Version 2.8 because it allows the import of data from engineering into Siemens TIA Portal via Automation ML (AML). The reference identifiers of the Festo components can be determined from the finished project and then used afterwards. These reference identifiers and other data – such as the symbolic addresses – can be written into the AML data that is exchanged with TIA Portal. Software data can be transferred back to the EPLAN project in the same way.
Background
Today, machine/plant documentation is often still stored as a paper copy in the control cabinet. Searching for faults in what is often more than 500 pages of documentation can be difficult and extremely time-consuming. A paperless workflow in this environment is more cost efficient and also improves quality. In addition, any changes made to the machine/plant often don’t get documented and, in the event of a malfunction, maintenance personnel only have access to outdated data/documentation. ©EPLAN Software & Service GmbH & Co. KG, April 2019
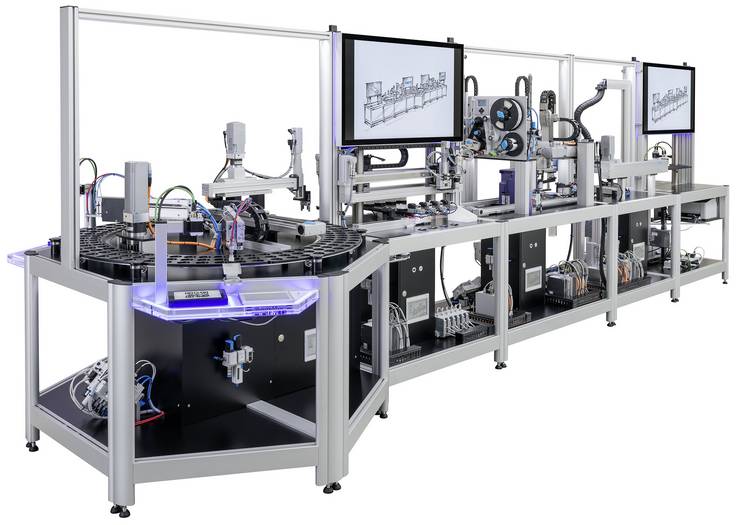
The Productivity Master, a modular demonstration system for individualised USB sticks from Festo, shows where automation technology in combination with digitisation will be developing along the value chain.
©Festo AG & Co. KG
More
- <link file:53429 download file>Download press kit
- <link>More on EPLAN eVIEW
- <link http: www.getdigitalnow.de _blank>www.getdigitalnow.de